도자기공업의 제조공정
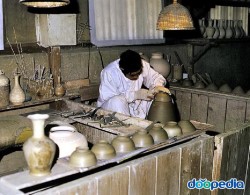
도자기 공예작업
도자기의 제조공정은 일반적으로 소지토(素地土:土)의 조제,
성형·건조·소성·유약칠·채식 등으로 나눌 수 있다.
⑴ 소지토의 조제: 한 가지 원료로 만들 경우에는 마른 소지토를 잘 분쇄하고
적당량의 물을 사용하여 잘 반죽하면 되지만, 두 가지 이상의 원료를 사용할
경우에는 혼합조제가 필요하다. 그 방법에는 건식과 습식이 있으며, 원료의
성질·처리방법·사용목적 등에 따라 알맞은 방법을 택한다. 건식조합(乾式調合)은
원료를 곱게 분쇄하여 원료별로 저장된 것 중에서 필요한 양을 각각 저울로 달아서
혼합하며, 이때 적당량의 수분을 첨가해서 균일하게 혼합이 되도록 잘 섞는다. 주로
재래식 방법에 의한 타일용 소지토 조제에 이용되었다. 습식은 백색 소지의 도기나
자기의 경우에 주로 이용되며, 수비한 점토와 각각 미분쇄한 원료들을 적당량씩
달아서 혼합하고 물을 사용하여 이장(泥漿:slip)으로 만들어 잘 저어서 균일하게
배합이 되도록 한다.
이 방법 외에 근래에 많이 사용되는 것은 괴상(塊狀)의 원료들을 조 크러셔(jaw
crusher) 또는 플랫 밀(plat mill)로 조분쇄·중간분쇄한 각 원료의 필요량과
점토의 적당량을 달아서 적당량의 물과 함께 볼 밀(ball mill)에 넣고, 미분쇄와
동시에 혼합하는 방법을 주로 택하고 있다. 볼 밀은 두꺼운 철판으로 된 원통형의
내면에 규석이나 자기의 블록을 붙이고 그 속에 프린트구(球)를 넣은 것이며,
원료와 물을 넣고 회전시키므로 원료의 마쇄와 혼합을 동시에 할 수 있게 되어
있다. 용량이 큰 것은 5∼6t이 되는 것도 있다.
근래에는 철통 내부에 내장석 대신 고무판을 입힌 것도 있다. 볼 밀 속에서
마쇄되어 혼합된 이장은 체로 거르고, 탈철기를 통과시켜서 철분을 제거시킨 다음,
콘크리트로 된 탱크에 옮겨 교반하면서 펌프로 여과기에 보내어 탈수한다. 탈수된
소지토는 진공토련기(眞空土練機)를 사용하여 다시 잘 반죽하고 소지토 속에 섞여
있는 공기를 빼낸 다음 일정기간 동안 저장하였다가 사용한다. 근대적이고 대형화된
공장에서는 성능이 우수한 진공토련기를 사용하며, 이 토련기를 거쳐서 나온
소지토를 바로 사용하기도 한다.
⑵ 성형:도자기의 성형방법으로는 물레성형(jiggering), 주입성형(casting),
압출성형(plastic forming by extruding), 압착성형(pressing)의 네 가지가
중요하다.
① 물레성형:진공토련기에서 이긴 배토를 써서 물레로 성형하는 방법이며,
손물레성형과 기계물레성형이 있다. 손물레성형은 물레 위에 배토를 놓고 물레를
돌려가며 손으로 빚어서 형상을 만드는 것이다. 비능률적이어서 공업적으로는 거의
쓰이지 않는 방법이지만, 공예품 성형에는 아직도 많이 쓰인다. 기계물레는
석고틀에 배토를 놓고 물레를 돌려가면서 틀과 주걱 사이에서 성형되도록 하는
것으로, 식기류나 용기류의 제조에 가장 많이 쓰는 방법이다. 이 방법도 기계물레를
사용한다는 것 이외에는 수공이 많이 드는 방법이며, 배토에서 완전 성형까지의
조작을 자동화하여 이 공정 전부를 기계화한 자동기계 물레방식이 최근에 채택되고
있다.
② 주입성형:점토나 소지원료에 물을 넣어 손으로 이겨서 반죽하면 연토가 되고,
다시 물을 더 가하면 반죽은 유동성을 띠게 되어 용기를 기울이기만 해도 수월하게
다른 용기에 옮길 수 있게 된다. 여기에 다시 물을 가하면 가는 입자가 물 속에
현탁(懸濁)되어 있는 상태가 되어 액체와 같은 성질을 가지게 된다. 이와 같이 한
것을 이장이라고 한다. 이장을 석고틀에 주입하여 성형하는 방법을 주입성형이라고
한다. 이장을 석고틀에 주입하면 석고틀은 물 속에 현탁하고 있는 분체를 물과 함께
틀의 표면에 끌어들이고, 끌어들인 물은 석고의 내부에 확산 흡수되며, 틀의 표면에
수분이 적은 이장의 층이 생긴다.
시간이 경과하면 이 이장의 층은 굳어지고 두꺼워진다. 이와 같이 굳어진 이장의
두께가 적당히 된 다음에 남아 있는 이장을 쏟아버리면, 굳은 이장의 층만이
석고틀에 붙게 된다. 이 부착층은 탈수될수록 수축하고 견고하게 되므로 석고틀을
뽑아내면 성형된 소지가 남는다. 이와 같은 주입성형은 주로 다른 방법으로는
성형하기 어려운 복잡하고 정밀한 물체를 성형하는 데 쓰인다.
③ 압출성형:손으로 이겨서 만들 수 있는 상태의 물을 포함하고 있는 배토로
성형하는 가소성 또는 소성성형의 일종으로 함수량은 대개 15∼25%이다. 이러한
배토를 진공토련기와 같은 압출장치로 압출하여 연속적으로 성형하는 대량생산에
적합한 방법이다. 단면이 균일한 것, 즉 단면이 원형·반원형·다각형인 것들을
성형할 수 있다. 단면이 작아서 1단 압출로는 곤란한 것은 2단 압출로 하며, 또
압출성형한 것을 반건조상태나 건조상태로서 다시 선반가공으로 성형을 완료하는
수도 있다.
④ 압착성형:배토를 압착기와 틀을 써서 가압하여 성형하는 방법이다. 그러나 이
방법은 주로 반건식 이하의 가소성이 적은 배토를 이용하여 성형할 때 쓰며, 마찰
프레스와 수압 또는 유압 프레스를 가장 많이 이용한다.
⑶ 건조:성형물은 수분을 제거하여 가마재입(再入)에 필요한 강도를 주고, 소성을
위험 없이 빠르게 하기 위하여 건조하여야 한다. 성형물 건조의 제1단계는
점토입자에 윤활제 구실을 하는 물의 제거 단계이다. 물의 증발은 표면에서
일어나는 것인데, 점토입자간의 틈은 서로 불규칙적이지만 모세관으로 되어
있으므로 내부의 물은 이 모세관을 통하여 표면으로 이동되고 계속 증발한다.
그러므로 미립자가 많은 가소성이 큰 점토를 많이 함유할수록 모세관은 가늘어서
건조에 오랜 시간이 걸린다. 이와 같이 점토입자의 활재로 되어 있는 수분이 나감에
따라서 점토입자는 접근하여 부피가 줄어들고 수축이 계속된다. 그러나 좀 큰
입자가 서로 접촉하게 되면 수축은 거의 완료된다. 이때 달아나는 물을 수축수라고
하며, 이때까지의 건조에 특히 조심하여야 한다. 나머지 틈에 있는 물도 역시
증발하여 달아나며, 이때에는 수축은 거의 일어나지 않고, 물이 달아난 자리는 틈이
생긴다. 끝으로 입자의 표면에 흡착되어 있는 물 피막의 제거이다.
그러나 이 물은 표면적(겉넓이)은 크지만 입자에 강하게 흡착되어 있으므로 상당히
높은 온도로 건조하여야 하며, 특히 입자가 작으면 작을수록 건조가 어렵다.
결과적으로 건조공정에서 가장 주의하여야 하는 과정은 수축수가 증발하는 단계, 즉
수축현상을 수반하는 건조과정이다. 건조장치로는 온돌형·상자형·터널형 등 여러
가지가 쓰인다. 상자형에서도 건조선반이 이동식으로 되어 있는 물티제트 건조기가
많이 쓰인다. 이것은 많은 분사공이 달린 판을 통하여 최적의 건조조건으로 조절된
공기를 피건조물에 수직으로 분사 통과시켜서 건조하는 장치이다. 터널형으로는
소성용 터널가마에서의 폐열을 이용하는 열풍식 터널가마가 가장 많이 쓰이며,
이것은 소성용 터널가마의 냉각대에서 약 140℃ 정도의 열풍을 한쪽에서 끌어넣고
다른 한쪽에서 방출한다.
⑷ 시유(施釉):유약(釉藥)은 유라고도 하며, 유약을 소지에 입히는 것을 시유 또는
유약칠이라고 한다. 시유는 소지 표면에 광택을 주어 더욱 아름답고 돋보이게 하여
미적 장식효과를 높이는 목적과 표면을 매끄럽게 하여 오염을 방지하고, 흡수성을
없애 물이나 화학약품에 대한 저항성을 증대시키는 데 있다. 미적 효과를 더욱 크게
하기 위해서는 소지에 조각한다든지 유약을 칠하기 전에 채료(彩料)를 사용하여
그림이나 문자, 그 밖의 채색(밑그림, 바닥그림 또는 무늬넣기라고 한다)을
한다든지, 또는 유약 위에 색유(色釉) 또는 채료를 사용하여 채식(彩飾:윗그림)하는
방법 등이 이용된다.
유약은 기물에 입혀서 소성하면 녹아서 소지에 밀착하는데, 만일 소지의 팽창률
또는 수축률과 일치하지 않으면 잔금이 생기거나 유약이 떨어져 나간다. 용융온도에
따라서 연질유와 경질유로 크게 분류되며, 연질유는 도기에 널리 사용되며, 특히
낮은 온도에서 녹는 납성분이 많은 유약을 납유약이라고 하여 조도기·토기 등에
많이 사용한다. 경질유는 주로 자기에 쓰이며, 불투명유는 목적에 따라
아비산·안티몬·주석·아연·티탄·골회 등을 적당히 배합하여 사용한다. 색유는
모든 유약에 무기색소의 구실을 하는 코발트·크롬·철·구리·니켈·망간 등이나
적당량의 무기질 채료를 첨가하여 착색한 유약이며, 청자유·진사유 등도 색유의
일종이다.
또한 윗그림용 채료도 저온에서 융착하는 색유이다. 일반적으로 사용하고 있는
시유방법은 담금법으로서, 유약을 이장으로 만들고, 이 이장 속에 성형하여 건조된
또는 초벌구이한 소지를 담그고, 소지의 흡수성을 이용하여 소지체 표면에 유약을
입히는 방법을 사용하고 있다. 이 때 유약의 두께는 소지의 흡수율, 이장의 농도,
담그는 시간에 따라 다르므로 잘 조절하여야 한다. 표면에 요철(凹凸)이 있는
소지(조각을 한 것 등) 또는 소지의 두께가 두꺼운 것에는 압착공기를 사용한
분무법을 사용한다. 근래의 타일 또는 위생도기 등의 시유에는 분무법을 주로
사용한다.
⑸ 채식:도자기의 채식방법으로는 ① 소지의 장식적 성형방법, ② 색소지에 의한
방법, ③ 소지의 전면 또는 일부에 채식하는 방법, ④ 유약에 의한 방법, ⑤
밑그림에 의한 방법, ⑥ 유약에 채화하는 방법, ⑦ 유상에 채식하는 방법 등이
있다. 특히 유약에 의한 방법 중에는 ㉠ 투명유약에 의한 방법, ㉡ 불투명유약에
의한 방법, ㉢ 색유약에 의한 방법, ㉣ 마트유약에 의한 방법, ㉤ 결정유약에 의한
방법, ㉥ 균열유약에 의한 방법 등이 있다. 이와 같은 여러 방법이 단독 또는
겸용으로 이용되고 있으며, 이 중에서도 가장 널리 이용되고 있는 것은
유하채식법·유상채식법·색소지법 등이며, 이것들은 모두 색에 의한 장식이므로
이에 이용되는 채료가 가장 중요한 위치를 차지한다. 근대화된 대량생산체제의
공장에서는 전사지를 이용한 전사지법이 성행되고 있다. 미술자기 또는
도예계통에서는 재료를 붓을 이용하여 소지표면에 직접 채식·채화하는 방법도
이용되고 있다.
⑹ 소성:소성은 도자기의 제조공정에서 가장 중요한 단계이며,
소지·유약·모양·크기·용도, 또는 가마의 종류·연료·소성온도·불꽃 등의
조건에 따라 다소의 차이는 있지만 ① 겉구이(biscuit fire), ②
광택구이(본구이:glost fire), ③ 채식구이(decorating fire) 등으로 분류된다.
겉구이는 그 목적에 따라서 둘로 나눌 수 있다.
하나는 초벌구이라고도 부르는 것으로 자기제조에 주로 쓰이는 소성이다. 이는
소지에 채화한다든지 유약을 칠한다든지 하는 쉽고 안전하게 취급하기 위해 필요한
강도를 주기 위하여 800∼900℃ 정도의 낮은 온도로 소성하는 것을 말한다. 그러나
두꺼운 기물이나 큰 기물은 이 초벌구이를 하지 않는 수도 많다.
다른 하나는 체소(締燒) 또는 겉구이라는 것으로, 도기제조에 주로 쓰는 소성이며
초벌구이보다 훨씬 높은 온도(대개 1,100∼1,250℃)에서 소성한다. 이것은 소지가
기계적 강도를 충분히 가지도록 하고, 녹는점이 낮은 유약을 시유한 다음에 낮은
온도로 구워서 제품을 만들 목적으로 하는 소성이다. 광택구이도 초벌구이의 종류에
따라서 두 가지로 분류된다. 즉 초벌구이를 한 소지에 유약을 칠하여 광택이 날
때까지 소성하는 방법을 참구이라고 하며, 주로 이러한 소성방식은 자기제조에
쓰인다. 따라서 이 참구이는 보통 고온소성이 되며, 일반자기에서는
1,250∼1,410℃로 하고 있다.
이에 반하여 체소한 소지에 녹는점이 낮은 유약을 칠하여 비교적 낮은 온도에서
소성하여 광택을 내도록 하는 소성을 유약구이라고 한다. 일반적으로 유약구이의
온도는 체소온도에 비하여 100℃가량 낮은 것이 보통이다. 이와 같은 소성방식의
차이 때문에 자기와 도기는 성질상 여러 차이가 나며, 자기는 도기에 비하여 기계적
강도가 세고, 화학적 내구력도 강한 반면에, 치수를 정확하게 하기 힘들고, 채식도
좀더 제한되어 외관상 좋은 것을 만들기 힘들다는 어려운 점이 있다. 채식구이는
광택구이를 한 제품을 장식하기 위하여 유상채색료로 채화하든지 전사지로 전사해서
머플가마에서 낮은 온도로 소성하여 유상채료를 융착시키는 소성이다. 이
채식구이의 온도는 보통 700~900℃이다. 이 온도까지는 안정된 채색료가 많아서
거의 임의의 채색이 가능한다. 따라서 자기·도기를 막론하고 많이 채택하는
방법이다.
이들 도자기를 소성하는 장치에는 여러 가지가 있는데, ① 소성작업, ② 불꽃의
진행방법, ③ 불꽃과 피가열체의 접촉방법, ④ 사용연료의 종류, ⑤ 용도, ⑥ 형상
등에 따라 여러 종류가 사용된다. 한국에서 많이 사용되고 있는 가마를 보면
오름가마(등요)·꺾임불꽃식가마·터널가마 등이 있으며, 연료로는
벙커C유·경유·가스 등이 주로 쓰인다.